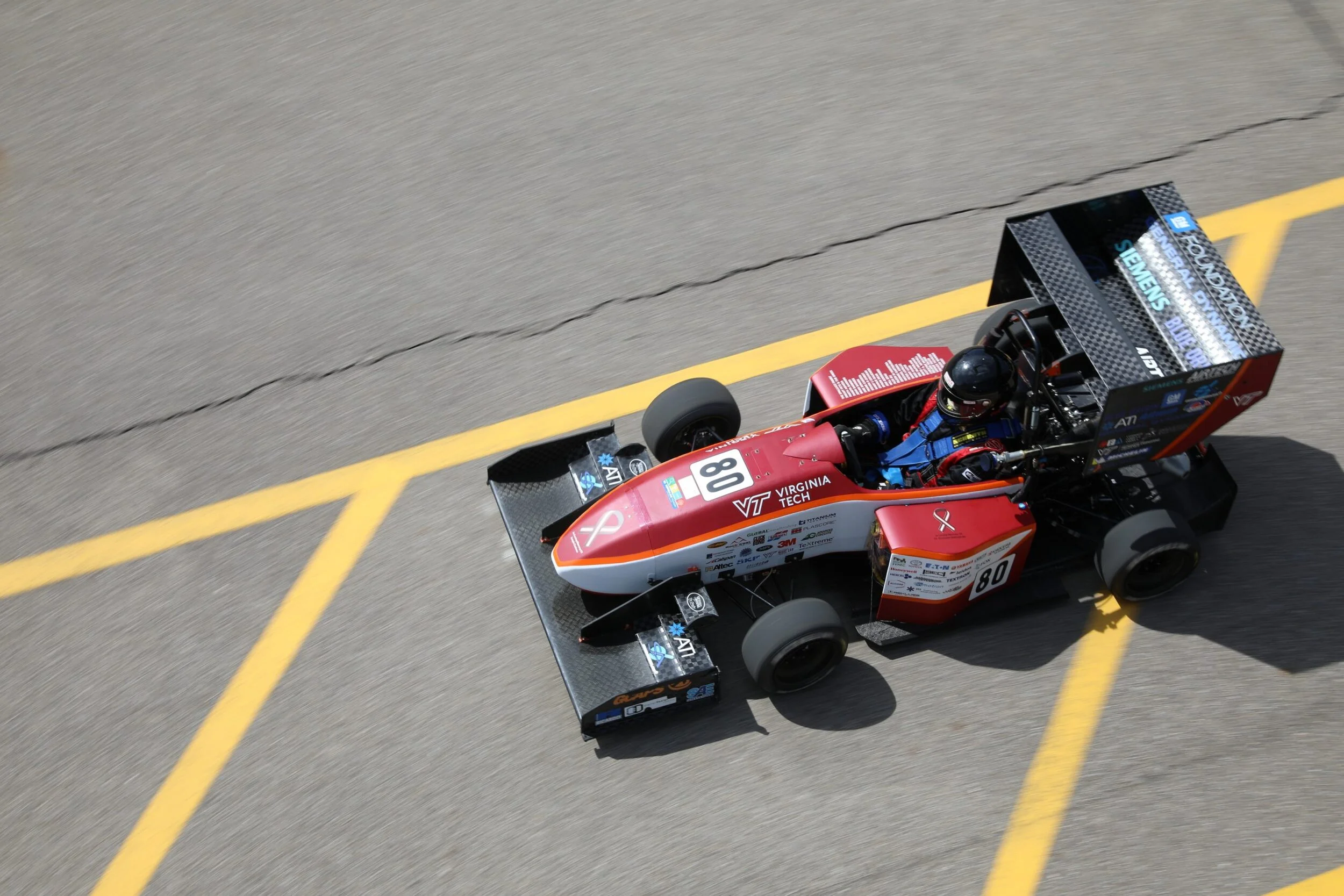
Formula SAE
Two half-size, formula-style race cars. Designed, built, and raced by students.
Virginia Tech Motorsports participates in Formula SAE’s electric and internal combustion vehicle competitions. The 2018-2019 team consisted of 60+ students from multiple engineering backgrounds working in a highly integrated environment.
Design
As a part owner in the aerodynamics subteam, I helped design and model aerodynamic structures using 3D CAD and FEA tools. Parts and simulations were integrated with other subsystems to perform full-architecture analysis.
Build
At Virginia Tech, most parts are machined and assembled in-house. I helped manufacture aerodynamic structures using composite materials, welded structures, and bonding techniques. Working closely with other subteams, these structures were assembled with the rest of the vehicle.
Test
All aerodynamic structures were tested using student-developed procedures. I participated in wind tunnel, structural, and track tests using university facilities. Test results were compared against model predictions to improve said models and optimize design.
Composite Materials
Front and rear wings were manufactured out of a lightweight foam core reinforced with multiple layers of carbon-fiber, while the nosecone used a honeycomb core. These carbon-fiber layers were bonded using resin and hardened using a custom-built oven and vacuum system.